#VCOM today - 4: Interfacing with technicians on site: Outlook? WhatsApp?
The question is: How do you, as an O&M manager or technical asset manager, interface with your counterparts? For example with your technicians on site?
Tools like Outlook have been present in our daily life for years. WhatsApp or WeChat are becoming popular tools in business as well. And yes - there are advantages to using these tools. We are used to them. Everyone uses them. And they are pretty easy to use.
Take a second and create a clear picture for yourself: How do I interface with my counterparts? Do I also feel, that our communication is shifting more and more to tools like WhatsApp?
Besides the advantages these tools definitely have, lets think about the disadvantages.
- Is the conversation secure? Who else could have access to my conversations?
- Is the conversation transparent to my colleagues if I am out sick?
- Is the conversation trackable and is it possible to evaluate reaction times for example?
- Is the amount of conversations I have on a daily basis structured in WhatsApp? And do I see the status of all my conversations on one single screen?
I assume you would agree. The answer to all these questions is No. So, what else could we do?
It is just a few weeks ago when the panelists at the Solar Asset Management Europe conference had a virtual debate about what to improve in the O&M and Asset Management business. Two points were absolutely common sense:
- Standardization of processes
- Digitalization of interfaces
Again, it is too important to read it once only:
- Standardization of processes
- Digitalization of interfaces
I know, it is hard to start thinking in a new way and to change processes. Even harder to change how your colleagues and yourself work together. Believe me, in the long run, it is worth it to start doing it.
I would like to inspire you with a wonderful tool that can help you to reach the next level of communication - internally and externally.
The VCOM Ticket and VCOM CMMS System
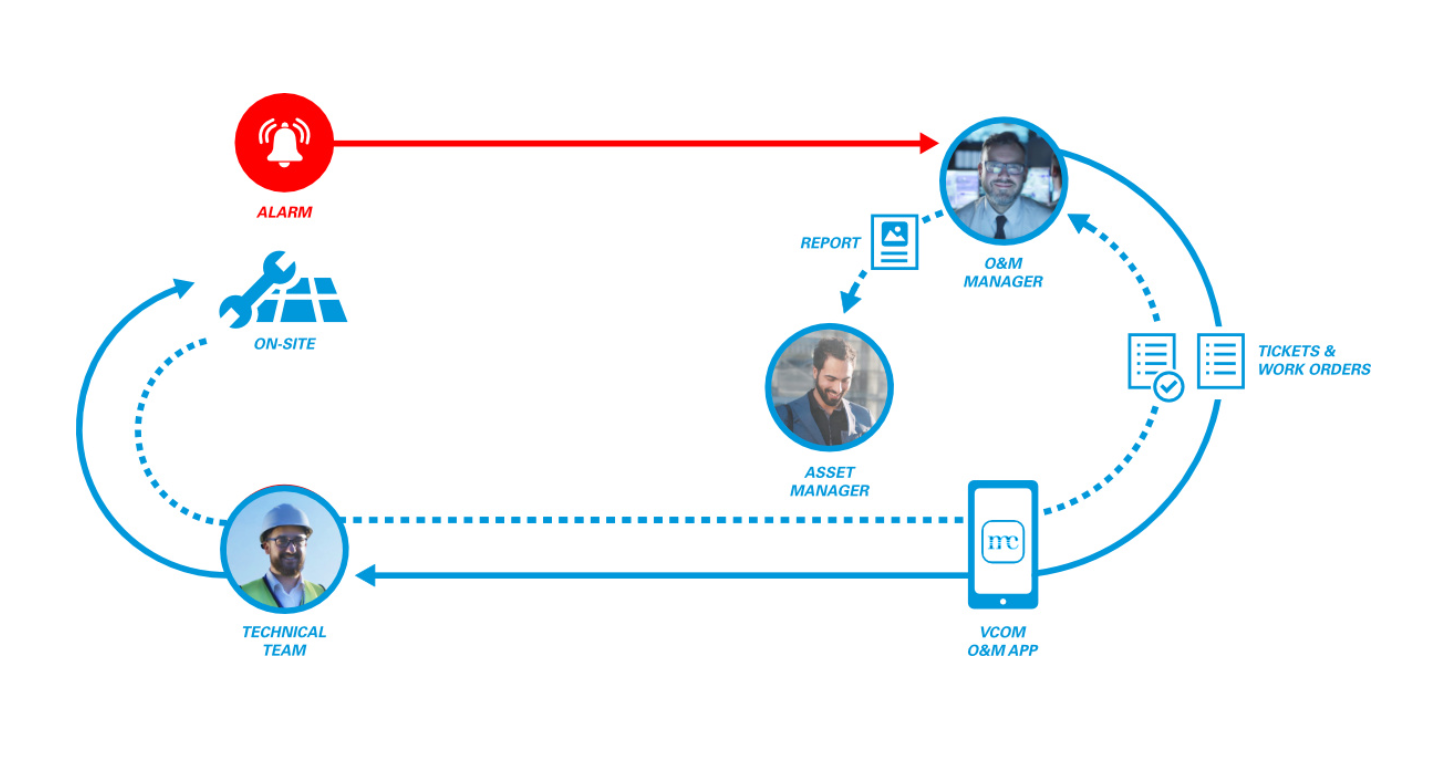
Lets pick one example we all know from daily business. You are on the way to ask your partners or colleagues, responsible for the on site work, to go schedule the yearly maintenance. The yearly maintenance tours of technicians are often pretty long. Day by day, new plants and lots of information to collect and to structure.
Today, the real life is as follows: Technicians get an e-mail with the info, that they have to go for the yearly maintenance. Maybe the e-mail also includes a description of what to do. The technician goes on site, takes pictures, makes hand-written notes and finds defects. He or she comes home late and is out of time to digitize the hand-written notes. Taking a photo of the hand-written notes and sending the photo to the O&M manager is easier. Congratulations to the O&M manager. It is his/her job now to translate hand-written notes in a format that can be used to report the maintenance to the owner of the plant.
What do you think: How long does this process often take? 2 days? 5 days? You are optimistic. I have often heard, that it takes weeks.
How to digitize workflows and avoid media discontinuity in 2021
The VCOM CMMS completely digitizes the process described above. You, as the O&M manager, are able to create yearly maintenance checklists for example, you can easily give to your partners then. Do this once, and you can use them again and again. Standardization is key here and increases the quality of your O&M processes sustainably.
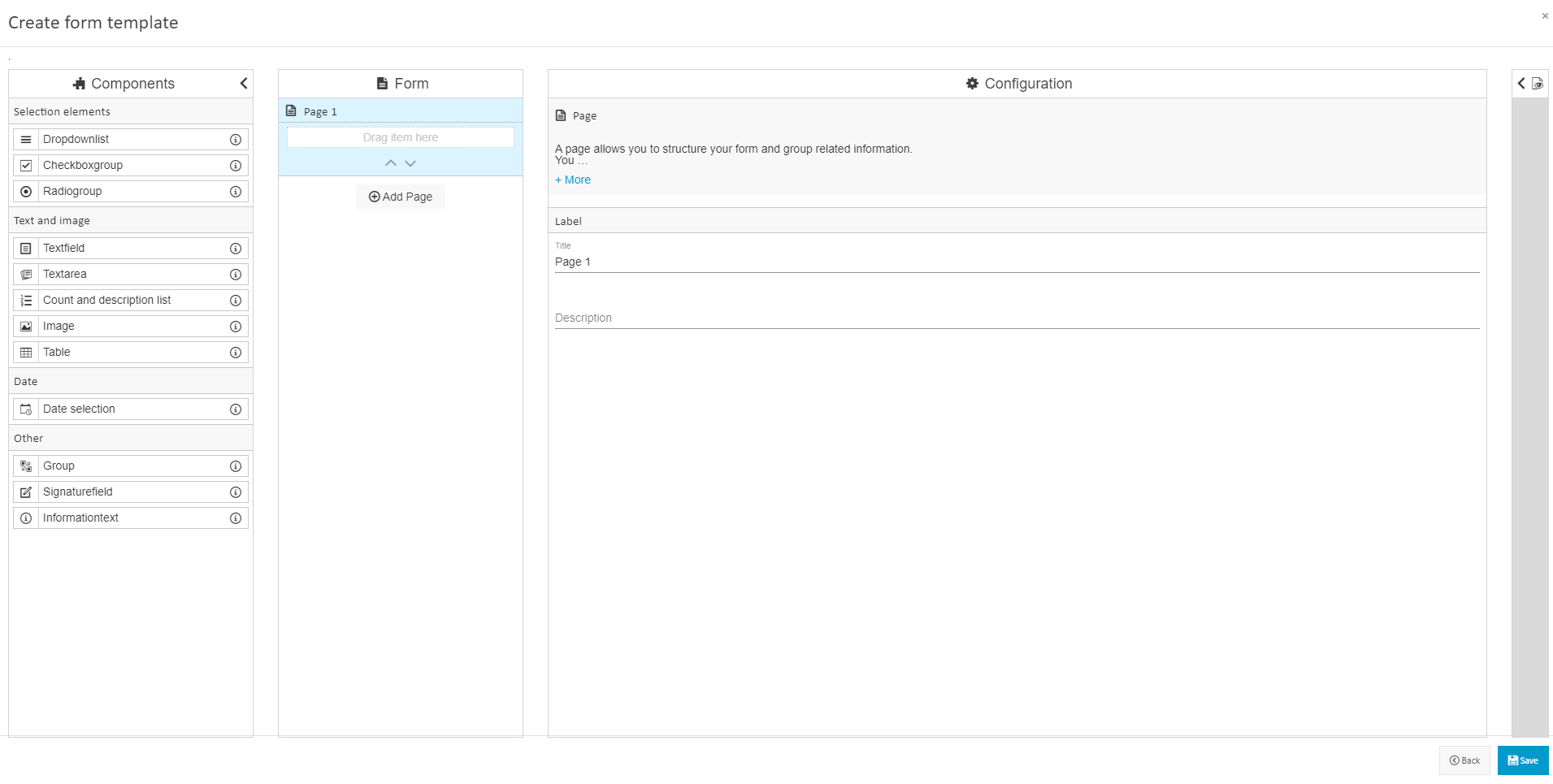
Picture: Solar PV specific checklist creation reflecting your workflow by 100 %
Now: Start the workflow by creating a work order. You can link several checklists to one work order. Contact details, the technician may need, are already part of the work order. Safety instructiuons can be added to the work order to avoid any health and safety issues with subcontractors. Add documents or pictures. All in all, hand over a work order with all relevant information for the technician. This avoids questions and speeds up the process.
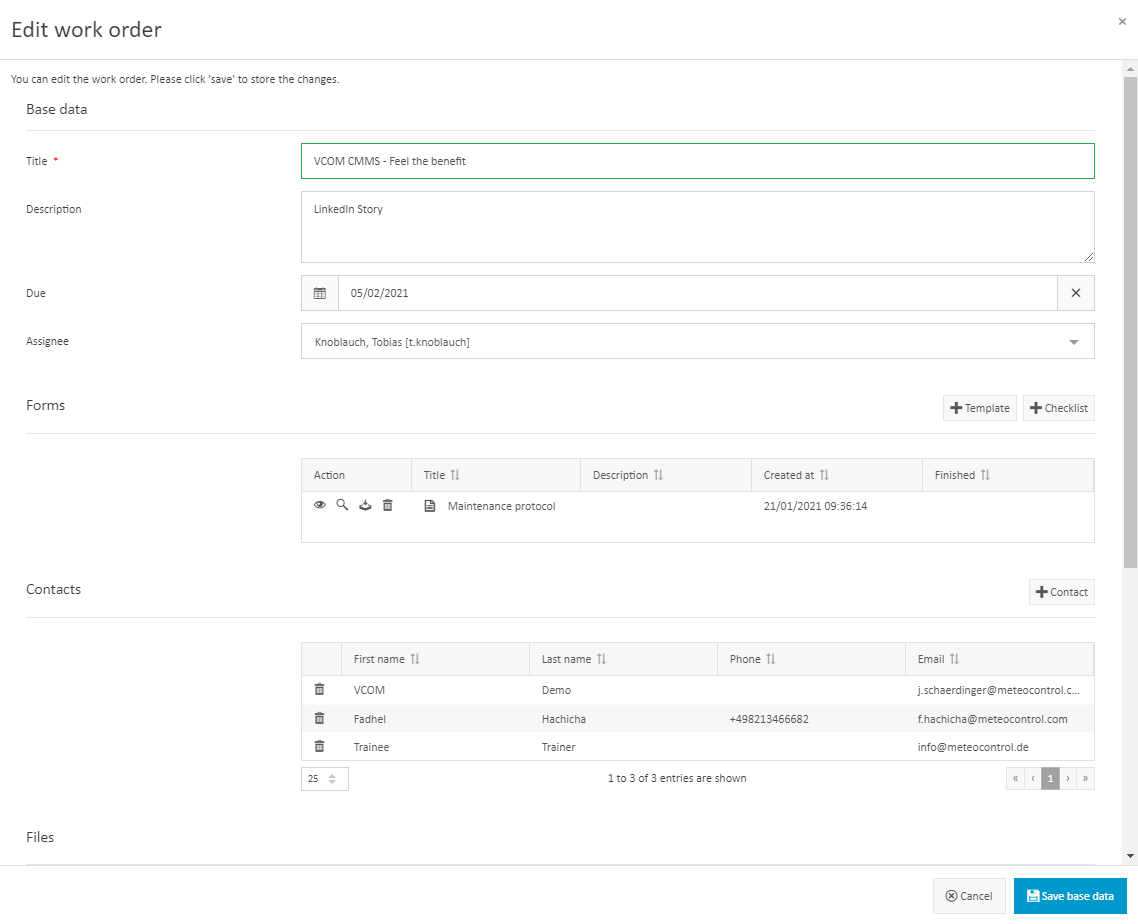
Picture: Setting up a work order and assigning the work order to a technician
The selected technician receives the checklists in the VCOM O&M App and he can already fill in the checklist and take photos in the App itself. No hand-written notes are needed.
After having done the on site visit, the technician can send back the notes incl. the time he spent on site etc. with just one click.
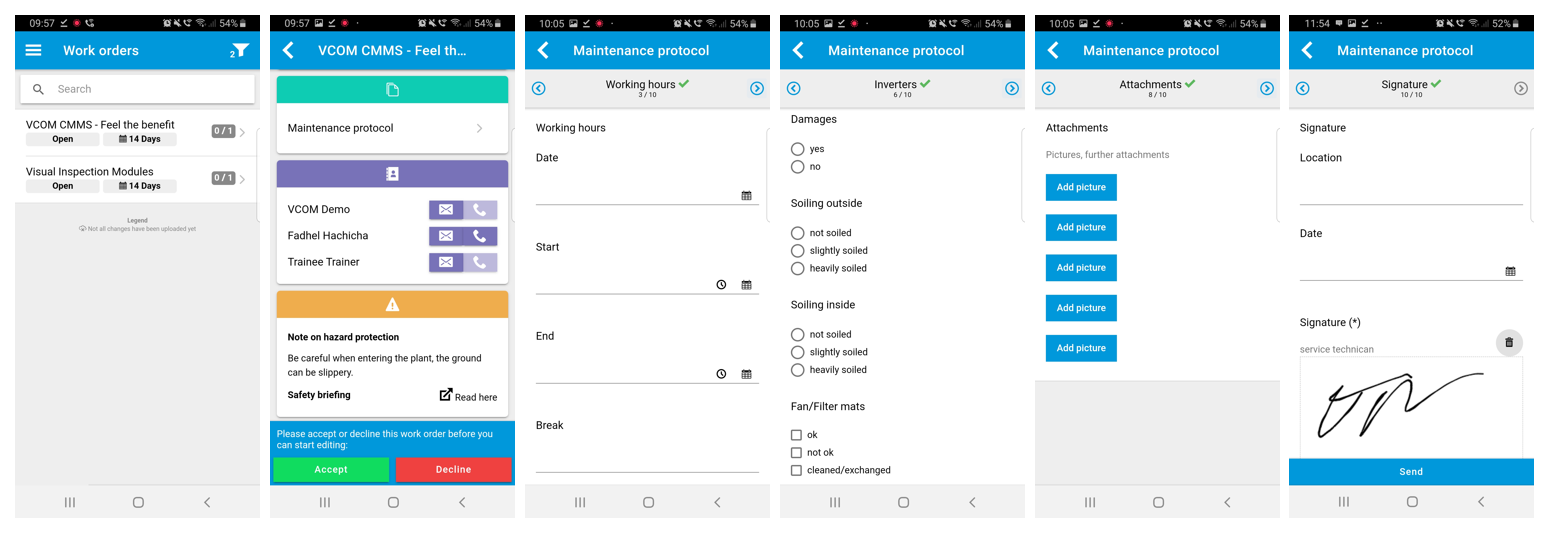
Picture: VCOM O&M App - Work Order
Are you happy already? Wait! The best is yet to come. The O&M manager can now create a maintenance report. Completely automated, after having defined a template once. If you are interested in how the final report can look like and how this can increase your customer happyness, feel free to contact me and and I will gladly share insights with you.
If we now have a look at the above mentioned points we wanted to optimize: We have optimized them! And welcome: You arrived in the new world of a much more standardized and digitalized O&M. You will be much more effective than your competitors and ready for the future!